In precision manufacturing, selecting the right machining method is more than a technical choice—it’s a strategic one. Understanding when to use CNC milling versus turning can save time, reduce costs, and improve the performance of your final parts.
At Jeek Rapid, we often see clients unsure which process best suits their designs. This guide breaks down the practical differences and gives you a framework to make smarter, faster decisions.
What Is CNC Milling?
CNC milling uses a rotating multi-point cutting tool that moves along multiple axes to remove material from a stationary workpiece. It’s particularly well-suited for prismatic parts, cavities, and intricate three-dimensional geometries.
Mills can operate on 3, 4, or 5 axes, allowing access to multiple surfaces in a single setup. The process supports a wide range of materials—from soft plastics to hardened metals—and offers strong design flexibility without requiring custom tooling.
What Is CNC Turning?
CNC turning involves rotating the workpiece itself while a stationary, single-point cutting tool removes material. This method is ideal for components with rotational symmetry, including shafts, pins, and bushings.
Compared to milling, turning delivers faster cycle times for round parts and produces smoother surface finishes along cylindrical features. It’s widely used in automotive, energy, and medical industries for both prototypes and high-volume production.
Key Differences Between Milling and Turning
Feature | CNC Milling | CNC Turning |
---|---|---|
Tool motion | Rotating cutter moves on multiple axes | Workpiece rotates against a fixed tool |
Ideal part shape | Flat faces, angular surfaces, pockets | Cylindrical or symmetric features |
Surface finish | Good, may require post-processing | Excellent on outer diameters |
Geometric complexity | High—supports 3D contours and undercuts | Moderate—best for round parts |
Setup complexity | More complex setups possible | Simpler setups and fixturing |
Production volume | Low to medium | Medium to high |
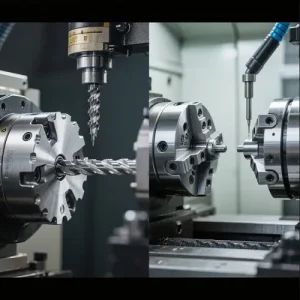
Design Considerations: Milling vs Turning
Not all geometries are created equal. When evaluating how to manufacture a part, design plays a pivotal role:
-
Choose milling for:
-
Parts with slots, grooves, or pockets
-
Flat faces with hole patterns or contours
-
Custom brackets, housings, and enclosures
-
-
Choose turning for:
-
Long shafts, threaded rods, and stepped cylinders
-
Rotational symmetry with tight concentricity
-
Round parts with minimal side features
-
When in doubt, submit your drawing to us for a free DFM review. Our engineers will recommend the best machining path based on speed, accuracy, and cost.
Cost Comparison: What Really Impacts Price?
The cost difference between milling and turning depends on geometry, setup time, material, and cycle duration—not just the hourly rate.
Factor | CNC Milling | CNC Turning |
---|---|---|
Setup time | Moderate to high | Low to moderate |
Tooling | Multi-axis cutters | Simpler, fewer tools |
Cycle time | Longer per part | Often faster |
Material waste | Can be higher | More efficient |
Complexity handling | Better for 3D parts | Better for symmetric parts |
Generally speaking, turning becomes more cost-effective in high volumes and milling is better for complex one-offs or low-quantity production.
Precision and Surface Finish
Both methods offer excellent tolerances—often down to ±0.01 mm when properly set up. However:
-
Turning naturally produces smoother outer diameters and is better for achieving tight roundness tolerances.
-
Milling excels at maintaining flatness and hole alignment, but may require secondary finishing for aesthetic surfaces.
When You Need Both: Hybrid Machining Workflows
Many parts don’t fall neatly into just one category.
Consider:
-
A shaft with a milled keyway
-
A round connector with side holes
-
A valve body that needs both concentric and angular features
We handle these using hybrid workflows, combining turning and milling operations in sequence or using multi-function machines. This reduces handling, improves accuracy, and shortens total lead time.
Industry Applications: What Do Professionals Use?
Industry | Typical Parts | Preferred Process |
---|---|---|
Aerospace | Structural brackets, engine housings | Multi-axis Milling |
Automotive | Shafts, bushings, spindles | CNC Turning |
Medical | Bone screws, implant holders | Turning + Milling Hybrid |
Electronics | Enclosures, connectors, brackets | Milling |
Robotics | Precision shafts, collars, couplings | Turning |
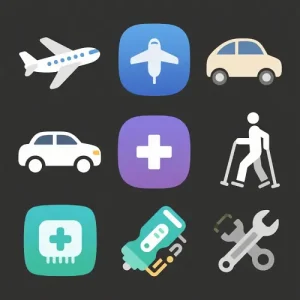
Material Compatibility
We machine most industrial and high-performance materials:
-
Common for Milling: 6061, 7075 aluminum, 316 stainless, titanium, PEEK, Delrin
-
Common for Turning: 4140 steel, brass, copper, PTFE, hardened tool steels
Each process requires unique tooling strategies, chip control, and coolant management—especially with exotic alloys.
Design Limitations and Engineering Pitfalls
-
Milling struggles with deep, narrow cavities due to tool deflection. Long end mills can vibrate, affecting tolerance and surface finish.
-
Turning requires enough length for clamping—short, wide parts can’t be securely held on a lathe.
-
Both processes must consider corner radii, thin-wall stability, and tool clearance during design.
We often help clients rework their CAD models for improved machinability—before they waste time or money.
Quality You Can Trust
At Jeek Rapid, quality is engineered into every part we produce. We are certified to ISO 9001:2015 and operate in alignment with ISO 13485:2016 standards—ensuring our workflows meet the stringent demands of the medical device industry.
This means our team is trained to manage traceability, documentation, and process controls for high-precision, compliance-critical parts.
Whether you’re machining titanium implants or structural aluminum housings, we’re ready to meet your specs.
Let’s Start with a Better Process
Understanding the difference between CNC milling and turning is one thing. Working with a team that makes the right call every time—that’s where we come in.
Whether you’re looking to prototype a new idea, refine a part design, or optimize production cost, we’re ready to help.
Request a Quote or contact our engineers for a free DFM review.